Chicago YIMBY continues its Sister Cities series covering innovative and skyline-defining projects in the Midwest with another trip to Detroit. We originally kicked off the series with coverage of the Hudson’s Site skyscraper earlier this year and we now return to take a look at the Exchange Building nearby at 338 Gratiot Avenue near Greektown. Developer and general contractor Barton Malow is working with global firms Thornton Tomasetti for structural engineering and Ghafari Associates on the architecture of the structure.
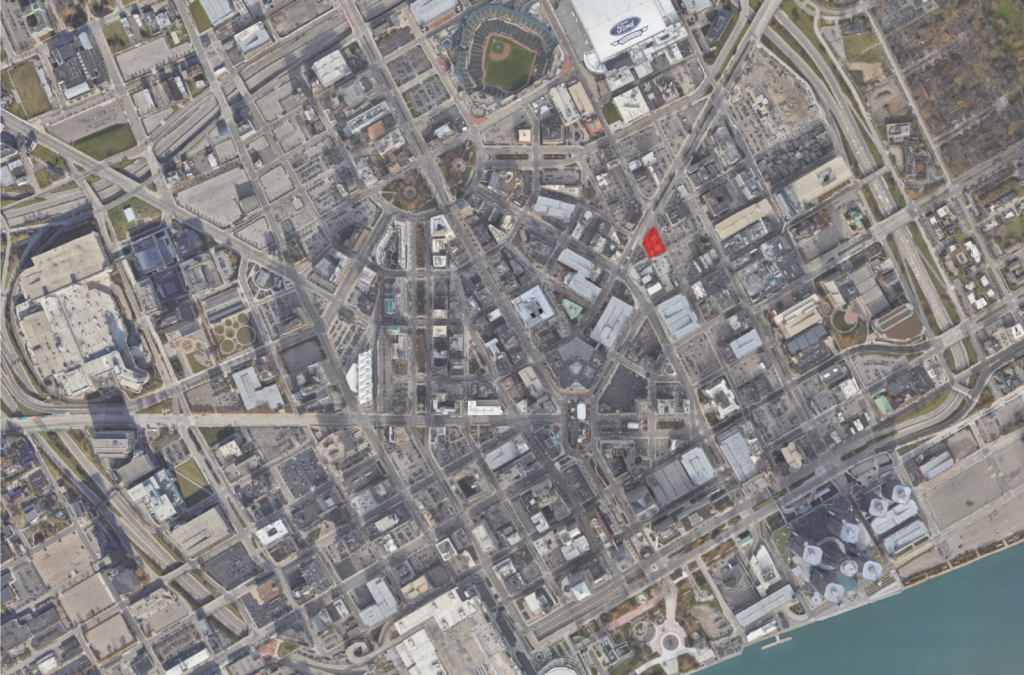
Site context map of The Exchange Building via Google Maps
With Detroit seeing a revival in demand for both office and residential space, various local organizations created a vision plan for connecting Greektown, known for its casino, to the central business district and entertainment area containing Ford Field and Comerica Park. This led to the decision to build a new mixed-use building on the small and odd-shaped site bound by the diagonal main thoroughfare to the north and the Detroit People Mover to the south creating a variety of logistical issues.
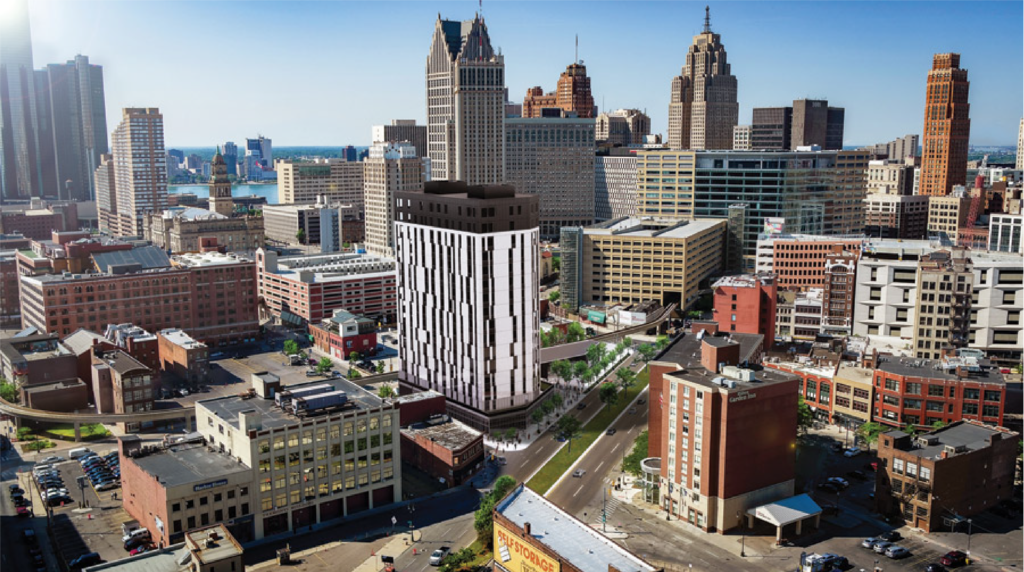
Rendering of the Exchange Building by Barton Malow
Rising 16 stories and 207 feet in height, the 166,000-square-foot Exchange Building is utilizing a top-down style of construction which took four years of research and 15 patents to get right. While not a completely new concept, it is the first time we see it in the US having been developed by LIFTbuild, a subsidiary of the tower’s Detroit-based developer. The closest concept deployed in Chicago will be at One Chicago where the ground floor was poured and vertical work started while they dug the basement levels simultaneously.
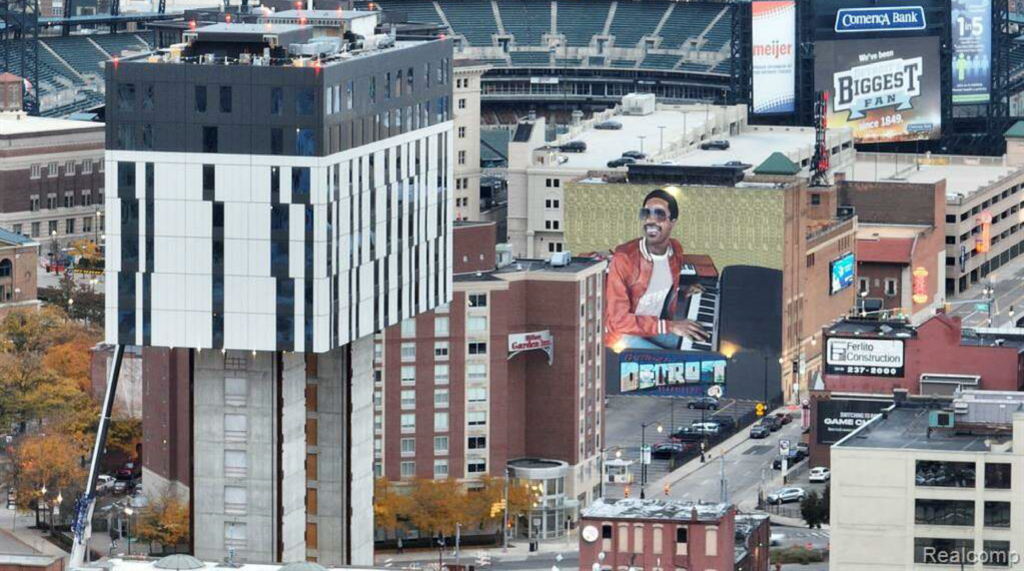
Recent image of the Exchange Building rising by Barton Malow via Engineering News Record
Since the site is just under three-fourths of an acre, the building’s construction began with the two concrete core towers being fully poured out to the top; these will carry all of the structure’s weight as the floors will be column-free and fully cantilever from the two. Once their 12-inch thick walls were completed, the top floor was built on the ground utilizing a steel frame and deck all of the floors will use. Each 11,000-square-foot floor plate contains 75 tons of steel and 110 cubic yards of concrete weighing around 500 tons with facade, MEP, and stud tracks laid out.
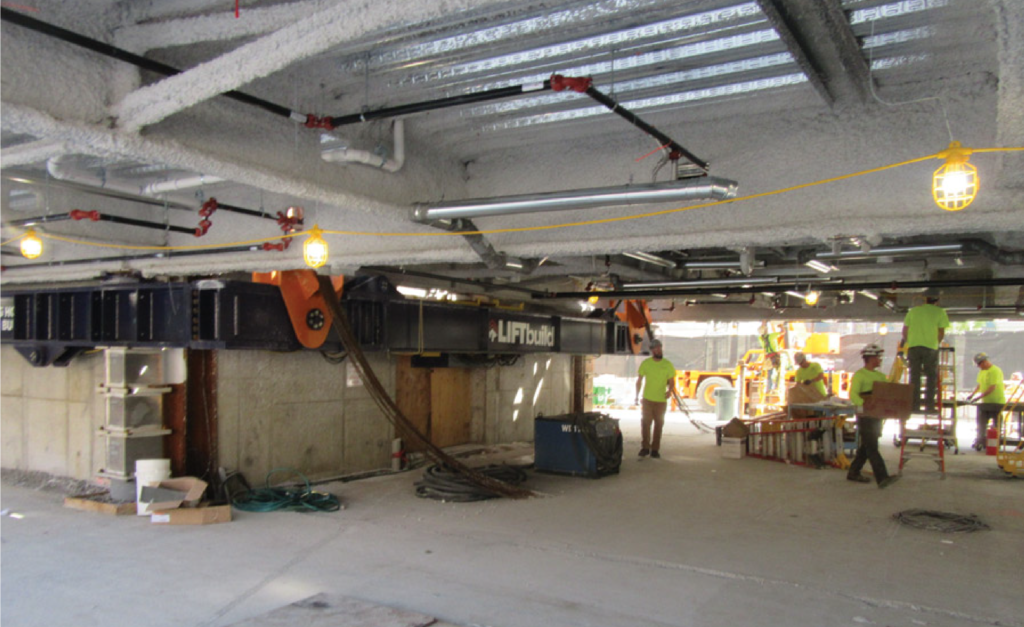
Construction of under-slab work prior to lift by Jeff Yoders via Engineering News Record
It then is slightly raised and the ceiling elements of the level below are installed on the bottom of the slab deck, marking the end of the section’s construction. This is when eight strand jacks with an individual capacity of 200 tons lift the floor up to place at a speed of 20 to 30 feet per hour, taking the 16th floor roughly 10 hours to reach its spot. Once each level does, they are bolted into place with the core before then internal walls and finishes can be built out in a fully enclosed space removing the need for any fall prevention and climate protection.
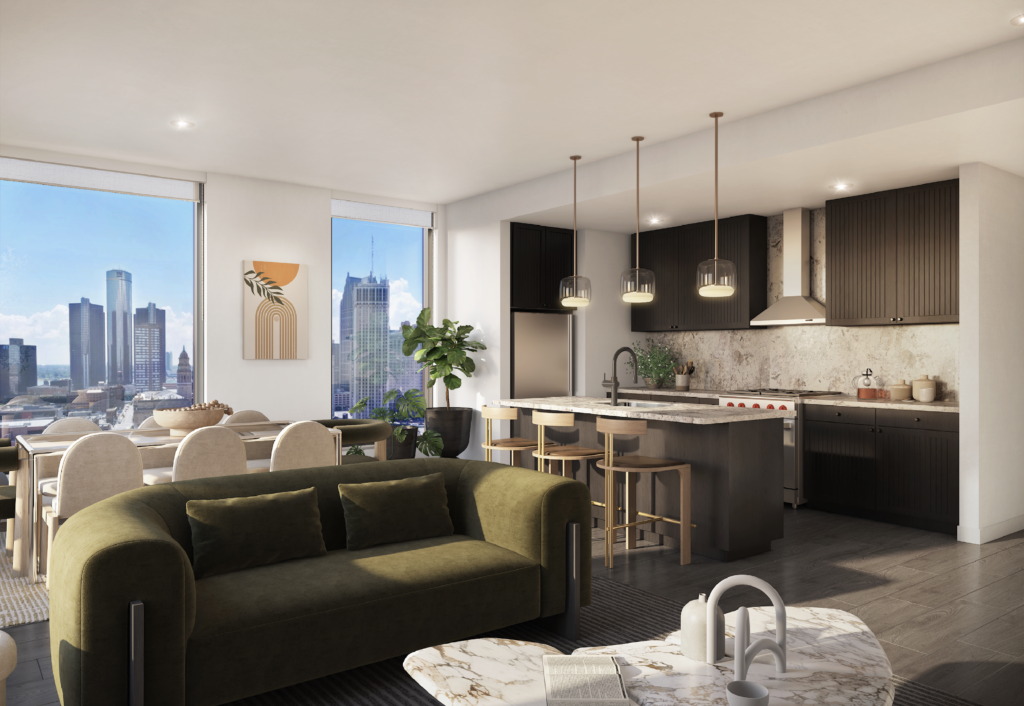
Unit rendering of the Exchange Building by Barton Malow
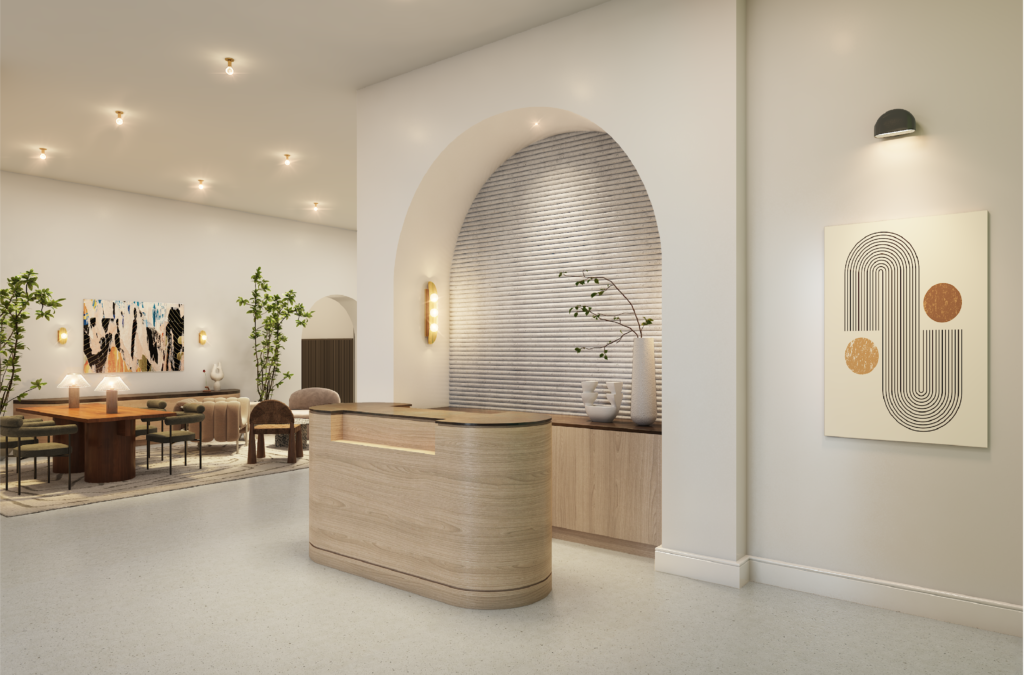
Lobby rendering of the Exchange Building by Barton Malow
When completed, the $64 million project will deliver 165 residential units split into 12 condominiums made up of one-, two-, and three-bedroom layouts starting at $500,000 and going up to $1.5 million in price. Occupying the lower levels will be 153 rental apartments made up of studio, one-, and two-bedroom floor plans ranging from $1,254 to $1,612 per month. The ground floor will also contain a small retail element at street level along with the entrance lobby.

Rendering of the Exchange Building by Barton Malow
All of this is being built with only 50 workers on site lowering overall cost, with the technique as a whole allowing for saving when installing complex mechanical systems which will be useful for medical buildings. With each floor requiring up to nine days to complete on the ground and a couple more to finish once lifted, the project will put up a floor around twice a month. This will allow for a swift completion after breaking ground this past spring, with expected move-ins to begin by late spring 2023.
More information on its construction and video of a floor being lifted can be found here.
Subscribe to YIMBY’s daily e-mail
Follow YIMBYgram for real-time photo updates
Like YIMBY on Facebook
Follow YIMBY’s Twitter for the latest in YIMBYnews
just kinda think it’s a little too white?!!
I think it looks nice, better than a parking lot
Just because it can be done doesn’t mean it should be done. This thing is atrocious based on final render.
Good stuff… Great to see some improvement to Detroit’s downtown.
Why are they doing top-first construction for this specific project? Is the cost benefit worth 4 years of research and 15 patents (which take time/money)? It doesn’t look like this building will have complex medical systems — but is there some site requirement that dictates this approach?
Hey waveland!
From my research it appears to be because of the small site, major roads surrounding it which can’t be closed, the position of the people mover tracks prevent it from being able to deploy a crane, as well as the developer inventing the tech used for it and wanting to trial it in order to market it towards others as well.
tall complex buildings are built all over Manhattan with real congestion and traffic….the “major roads” of Detroit can’t be as busy as Madison Ave/Park Avenue/Broadway in midtown NYC!! The trial reason might be more to the point….too bad the facade isn’t more fitting to downtown Detroit.
The technology and engineering is sooo freaking cool! Honestly it’s too bad the building is hideous. *Frownie Face*
It’s to prevent the workers from working at high levels which could cause some potential casualites